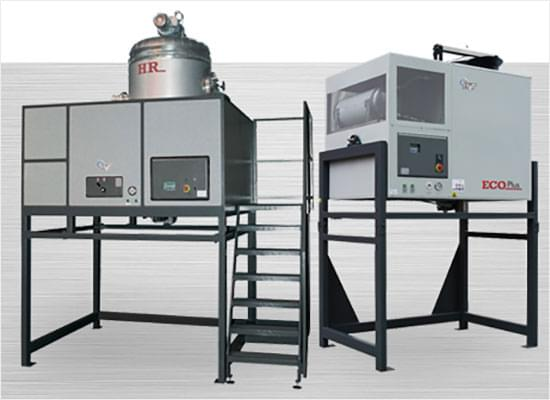
Solvent recycling is a game-changer for industries looking to save money and protect the environment. By reclaiming used solvents, companies can cut costs, reduce hazardous waste, and improve safety. This dives into the many benefits, technologies, and future trends.
Key Takeaways
- Solvent recycling helps companies save money by reducing the need to buy new solvents.
- Recycling solvents on-site cuts down on hazardous waste and the costs associated with its disposal.
- Advanced technologies like distillation and automation make the recycling process efficient and effective.
- Using solvent recycling systems can lead to a quick return on investment for businesses.
- Future trends include new technologies and a focus on sustainability and the circular economy.
Economic And Environmental Benefits Of Solvent Recyclers
Cost Reduction And Liability Mitigation
The process offers significant cost savings for companies. By reclaiming and reusing solvents, businesses can reduce the need to purchase new virgin solvents. This cuts down on material costs and minimizes expenses related to transporting and storing hazardous waste.
Additionally, it helps mitigate liability by reducing the volume of hazardous waste that needs to be managed and disposed of, thereby lowering the risk of environmental contamination and associated legal repercussions.
Reduction In Hazardous Waste
One of the primary environmental benefits is the substantial reduction in hazardous waste. By recycling solvents onsite, companies can significantly decrease the amount of waste that would otherwise be sent to landfills or incineration facilities.
This helps conserve landfill space and reduces the environmental impact associated with waste disposal. Moreover, recycling solvents reduces the need for new solvent production, lowering the demand for raw materials and energy and contributing to a more sustainable industrial process.
Return On Investment For Companies
Investing in recycling equipment can yield a high return on investment (ROI) for companies. The initial cost of purchasing and installing recycling systems is often offset by the savings generated from reduced solvent purchases and lower waste disposal costs.
Many companies find that the payback period for this equipment is relatively short, often within a few months to a couple of years.
Furthermore, the long-term financial benefits continue to accrue as companies consistently save on operational costs and improve their environmental compliance, making it a financially sound and environmentally responsible choice.
Technological Processes With Solvent Recyclers
Distillation And Separation Techniques
Distillation is a cornerstone in solvent recycling, separating solvents from contaminants. The process involves heating the waste solvent until it vaporizes. The vapor is then condensed back into liquid form, leaving impurities behind.
This method is highly effective for recovering solvents like acetone, alcohol, and toluene. Distillation efficiency can reach up to 99%, making it a reliable technique for solvent recovery.
Automation In Solvent Recycling
Automation plays a crucial role in modern recycling systems. Automated systems reduce the need for manual intervention, enhancing both safety and efficiency.
Features such as automatic loading and unloading, real-time monitoring, and error detection make the recycling process seamless. Automation improves operational efficiency and ensures consistent quality in the recovered solvent.
Integration Into Closed-Loop Systems
Integrating this into closed-loop systems maximizes resource efficiency. In a closed-loop system, the recovered solvent is directly fed back into the production process, minimizing waste and reducing the need for new solvent purchases.
This integration mainly benefits industries with high solvent usage, leading to significant cost savings and environmental benefits. Closed-loop systems also simplify regulatory compliance by reducing the volume of hazardous waste generated.
Operational Advantages Of Onsite Solvent Recyclers
Eliminating Dependence On Third-Party Services
Allows companies to reduce or eliminate their reliance on third-party waste management services. This independence cuts costs associated with outsourcing and provides greater control over the recycling process.
By managing recycling internally, companies can consistently ensure their specific needs and standards are met.
Enhancing Safety And Efficiency
Implementing on-site systems enhances safety and efficiency within a facility. Reducing the need to transport hazardous waste offsite minimizes the risk of accidents and spills during transportation.
Additionally, on-site systems streamline the recycling process, allowing quicker turnaround times and less downtime. This leads to a safer working environment and more efficient operations overall.
Reducing Labor And Operational Costs
Significantly reduces labor and operational costs. The need for manual handling of waste solvents is minimized, freeing up staff to focus on other critical tasks.
Automated recycling systems reduce labor requirements by handling the recycling process with minimal human intervention. This automation cuts labor costs and ensures a more consistent and reliable recycling process.
Case Studies Of Successful Solvent Recycling Implementations
Industrial Applications And Outcomes
Solvent recycling has shown remarkable success in the industrial sector. For instance, a large-scale manufacturing plant integrated an on-site system, which reduced the purchase of virgin solvents by 90%.
This not only cut costs but also minimized hazardous waste disposal. The plant reported a return on investment within just one year, highlighting the economic and environmental benefits.
Small And Medium Enterprises
Small and medium enterprises (SMEs) have also benefited. A mid-sized printing company adopted a recycling unit, which allowed it to reclaim 95% of its used solvents.
This significantly reduced its operational costs and waste management expenses. The company also noted improved workplace safety due to less handling of hazardous materials.
Large Scale Operations
Large-scale operations have seen transformative results. A multinational corporation in the automotive industry implemented a closed-loop solvent recycling system. This system enabled the company to recycle solvents continuously, reducing their need for new solvents by 85%.
The initiative saved millions of dollars annually and aligned with the company’s sustainability goals, showcasing the scalability and effectiveness of recycling in large operations.
Challenges And Solutions With Solvent Recyclers
Handling And Disposal Of Contaminants
One of the primary challenges is the proper handling and disposal of contaminants. These contaminants can include various chemicals, residues, and by-products separated from the solvent during the recycling process.
Improper disposal can lead to environmental pollution and health hazards. To address this, companies must implement stringent waste management protocols and invest in advanced filtration and separation technologies.
Regulatory Compliance
Another significant challenge is navigating the complex landscape of environmental regulations. Companies must comply with local, state, and federal regulations regarding the recycling and disposal of solvents.
Non-compliance can result in hefty fines and legal repercussions. To mitigate this risk, it is essential to stay updated with regulatory changes and invest in compliance management systems.
Technological Limitations And Innovations
While recycling technologies have advanced, limitations can hinder efficiency and effectiveness. For instance, some recycling methods may not be suitable for all solvents or contaminants.
However, ongoing innovations in the field are addressing these limitations. Emerging technologies such as advanced distillation techniques and automated recycling systems make it more efficient and versatile.
Future Trends In Solvent Recycling
Advancements In Recycling Technologies
The field is witnessing significant technological advancements. New methods, such as molecular recycling, are emerging. These methods use solvents, heat, enzymes, and even sound waves to purify or transform solvents at the molecular level.
These technologies can handle a broader range of waste materials and produce high-quality recycled solvents that can be reused in various industrial processes.
Sustainability And Circular Economy
Solvent recycling is becoming a crucial component of the circular economy. By reusing solvents, industries can reduce their reliance on virgin materials, conserving natural resources and minimizing environmental impact.
Policies and incentives encouraging sustainable practices and the adoption of advanced recycling technologies support this shift toward a circular economy.
Market Growth And Opportunities
The market is poised for substantial growth. Increasing environmental regulations and the rising cost of waste disposal are driving industries to adopt recycling solutions.
Companies that invest in these recycling technologies can expect a significant return on investment, as these systems reduce operational costs and enhance sustainability.
The market also sees increased collaboration between technology providers, industries, and policymakers to develop and implement effective recycling solutions.
Choosing The Right Solvent Recycling Equipment
Factors To Consider
When selecting equipment, it is crucial to evaluate several factors to ensure the system meets your facility’s needs. Key considerations include:
- Capacity Requirements: Determine the volume of solvent your facility processes daily to choose equipment with appropriate capacity.
- Type Of Solvent: Different solvents have varying properties; ensure the equipment can handle the specific solvents used in your operations.
- Space Constraints: Measure the available space to ensure the equipment fits comfortably within your facility.
- Budget: Evaluate the cost of the equipment, including installation and maintenance, to ensure it aligns with your financial plan.
- Regulatory Compliance: Ensure the equipment meets all relevant safety and environmental regulations.
Customization And Scalability
Customization and scalability are essential for adapting equipment to your specific needs. Consider the following:
- Modular Design: Opt for equipment that allows for easy upgrades and expansions as your needs grow.
- Custom Features: Look for providers that offer customization options to tailor the equipment to your specific processes.
- Scalability: Ensure the system can scale up or down based on your production demands.
Provider Selection And Support
Choosing the right provider is as important as selecting the right equipment. Here are some tips:
- Reputation And Experience: Select a provider with a proven track record and extensive experience in recycling solutions.
- Customer Support: Ensure the provider offers robust customer support, including installation, training, and maintenance services.
- Warranty And Service Plans: Look for providers that offer comprehensive warranties and service plans to protect your investment.